1) Introduction
Elipse E3 can be used as an OPC client as well as an OPC server. In this article, we will see how Elipse E3 can be used as an OPC client.
Using OPC Servers when developing projects that use drivers can be very opportune. Some of its pros are:
- Interface uniformity with different networks and protocols: when using OPC servers indifferent networks, access to process data in the supervisory is managed with no need to adjust each network’s drivers, thus saving setup time.
- Full integration with the network: most of the time, OPC servers are created by the device’s manufacturers, who will likely include all network features in this software; that is, when protocol changes are implemented, OPC will have been updated by the manufacturer.
- I/O drivers not required: depending on their complexity, the development of I/O drivers may take a lot of time, even months. In addition, the costs involved in this process are often prohibitive. Some devices or protocols may not have native Elipse drivers, but can support communication through OPC Servers.
- Integration between different supervision tools: OPC makes it simple to integrate different supervision tools. For example, Elipse SCADA can be working as an OPC Client on the network while E3 is working as the server, or vice-versa.
However, there are some cons that should be observed when implementing OPC systems:
- Speed of communication: OPC software’s performance may be slower than the performance of I/O drivers because OPC involves a larger number of systems.
- Higher processing demands: As well as using different programs, OPC servers also use Operating System services, which may require a larger investment in network machines or devices when the OPC Server is working remotely.
- Maintenance: maintenance of systems communicating in OPC introduces a greater number of variables into the process. Failures in the communication services in Windows, for example, can usually cause systems running OPC to stop.
2) Setup Procedures
The first step to establish OPC communication is to have an accessible OPC Server, installed either locally or remotely. For the procedure described here, we used a standard application, which can be created in E3 Studio. The OPC server is Siemens Simatic Net, installed in the same machine as E3 Server (locally).
To communicate with this software, Simatic Net software was installed and configured, and adjustments were made to establish communication with an Industrial Ethernet network.
To access a device via OPC, go to Organizer and insert a new OPC Client Driver (Fig. 1).

Figure 1 – Inserting an OPC client driver
Next, righ-click the OPC driver and access its Properties. A window will pop up; click Select… button on OPC Driver tab (Fig. 2).

Figure 2 – OPC driver’s properties
A new window will list all available OPC servers, wheter they are local or remote (Fig. 3). Notice that E3 will appear on this list of servers, but it will not be used in this exercise.
Select the server installed in your PC or on the network.

Figure 3 – List of available OPC servers
To make sure it has been properly set up, click Activate Driver–Information. A new window, displaying server data (version, status, etc.) and the local server time, will open to show if the communication was established correctly.
3) Tag Import
There are two ways you can use the values available in the OPC server. The first one is to execute the process manually, inserting groups, OPC tags and OPC Block tags individually, and setting them up as indicated by the manufacturer.
The second one is via tag import – a quick and efficient process of selecting which data will be monitored and controlled by the supervisory. To start importing data, you must first make sure the server is activated and the OPC driver is properly configured for your project. Then, activate the communication between OPC driver and OPC Server. This can be done in the OPC driver properties, or by right-clicking the driver and selecting Activate Driver.
After communication has been activated, select Import Tags (Fig. 4).

Figure 4 – Import Tags Option
One of the advantages of importing tags is that, when you do it, you can check immediately if the tags are correctly setup and available in the OPC Server. When data is set up manually, it may not be possible to know right away the exact location of the problem in the event of process failure.
In addition to a few filter options, the tag import window displays two data trees: Current Project and OPC Server. The second tree lists all tags available for the filter being used. When you locate a tag that must be used in E3, just click and drag it to the OPC group where it will be used, otherwise the tag will not be imported and communication with that tag will not occur.
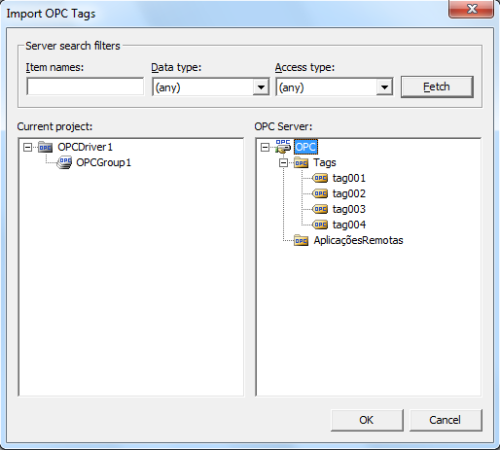
Figure 5 – Tags available during import
The organization of tags in groups can be very helpful for good communication performance. Other points should be noticed regarding communication, such as memory map organization, grouping similar types, etc. Another important item is the scan with which OPC Groups are read. This influences the application performance directly: the higher the tag’s priority, the shorter the scan time.
After importing the tags, click OK. You will notice that all imported tags will be listed in their groups just below the OPC driver.
To follow up tags values without launching the project, double click the OPC Driver. The list of driver tags will open on the right side of the E3 Studio working area. Activating OPC communication will list the tags values, which will be read according to the searching options setup of each OPC group.

Figure 6 – Tag communicating via OPC
The reading result will be in blue when the reading succeeds (Quality = 192), and in red when an error occurs. For example, Figure 6 shows a communication error with the selected tag because the PLC containing the network address was not available.
4) Final Remarks
Using OPC as your communication interface presents its pros and cons, which should be considered when the project is developed. Careful planning on issues such as tags quantity and memory mapping will, just like in any project, bring great benefits to OPC-based systems. This will ensure faster development, with fewer risks when compared to development involving drivers and protocols. In addition, since E3 is an OPC Client in all versions, the predicted investment in I/O drivers can be used for other purposes.