As atividades de extração mineral, notadamente a mineração industrial de uma maneira geral, visam à obtenção de produtos que devem ser adequados a processos subsequentes de refino. Estes processos, além das exigências em especificações químicas adequadas, também são limitados quanto à distribuição granulométricas dos minérios a serem tratados. Particularmente, para minérios de ferro, manganês, níquel, nióbio e etc, as especificações granulométricas ideais se concentram em faixas abrangendo as partículas de mais grosso calibre. Desta forma, toda a faixa granulométrica que engloba materiais de tamanhos menores do que certo limite, característico de cada processo, é considerada rejeito e assim descartada, seja como material de menor ou mesmo de nenhum valor comercial.
Algumas tecnologias de recuperação do tamanho médio granulométrico dos minérios, adequando-os aos processos de refino, foram desenvolvidas visando à otimização das atividades mineradoras e prolongamento da vida de minas em processo de exaustão. Várias tecnologias de aglomeração são disponibilizadas, tais como: briquetagem; pelotização; sinterização e etc. O processo de sinterização pode ser entendido como o fenômeno em que duas ou mais partículas sólidas se ligam pelo efeito do aquecimento à temperatura em que ocorre um inicio de fusão (fusão incipiente).
O enfoque da aplicação de tecnologias de informatização e automação de processos no setor será centrado no processo de sinterização, por ser um dos mais utilizados nas atividades de mineração de médio e grande porte.
2. Processos de Sinterização
Existem duas tecnologias básicas de sinterização: o processo GREENAWALT e o processo DWIGHT & LLOYD (ver Figura 4). O primeiro, intermitente, tem como unidade de produção uma panela basculável com fundo de grelha e forno de ignição móvel. O segundo é um processo contínuo, com um conjunto de caixas móveis, com fundo de grelha para carga e um forno de ignição fixo.
Basicamente, o mecanismo do processo de sinterização se desenvolve de maneira idêntica nas duas tecnologias. A unidade de produção, panela ou conjunto de caixas, é carregada intermitente ou continuamente com a mistura a sinterizar. A mistura contém, além do minério e adições metálicas, certa quantidade de combustível sólido e umidade. O combustível contido na mistura é inflamado pelas chamas e calor gerados no forno de ignição, iniciando uma combustão na superfície da mistura. O ar necessário à continuidade da combustão é aspirado, de cima para baixo, através da camada de mistura e das grelhas do fundo da panela ou do conjunto de caixas, por um sistema de exaustor/condutores de ar.
Quando a frente de combustão atinge as grelhas, todo o combustível presente na mistura a sinterizar deve ter sido consumido, gerado calor, vaporizado a água e calcinado os carbonatos, provocando uma semi-fusão e aglomerando todo o material carregado na panela ou caixa. O aglomerado assim formado em grandes blocos é então britado, peneirado e adequado às especificações do processo de refino do consumidor. Ainda assim, nesta etapa de britagem e peneiramento, tem-se uma parcela de material fino que é reciclado no processo sob o nome de finos de retorno de sínter.
O presente trabalho se restringirá ao detalhamento de funcionamento do processo DWIGHT & LLOYD (Figura 4), uma vez que as atividades de informatização e automação são praticamente as mesmas com pequenas adaptações.
3. Conjuntos Operacionais do Processo Intermitente
O esquema apresentado na Figura 2 pode ser subdividido, de uma maneira geral, em seis blocos operacionais com funções bem definidas:
3.1. Bloco de Ensilamento e Dosagem das Matérias-Primas
Neste setor, estão agrupados os silos de estocagem das matérias-primas que serão usadas no processo. É também neste setor que se desenvolve a atividade de controle da dosagem dos diversos materiais para a composição de um leito de sinterização previamente definido.
3.2. Bloco de Preparação da Mistura a Sinterizar
Esta é a etapa em que todos os componentes são misturados, visando à obtenção de uma mistura homogênea e um grau de micropelotização ideal para um bom desempenho do processo, em termos de permeabilidade.
3.3. Bloco de Ensilamento e Carregamento da Mistura
Este setor recebe a mistura pronta para sinterizar, armazenando em um silo pulmão, visando a um controle contínuo de abastecimento da caixa de sinterizar. Este abastecimento deve ser feito de maneira cuidadosamente controlada, através de um rolo alimentador, para se obter um máximo de permeabilidade durante o desenvolvimento subsequente do processo.
3.4. Bloco de Ignição da Mistura a Sinterizar
Imediatamente após o enchimento das caixas de sinterizar, neste setor, é promovida a ignição superficial do combustível sólido (coque ou carvão vegetal) incorporado à mistura que é considerado o motor térmico do processo.
3.5. Bloco de Sinterização
Este setor engloba o Exaustor Principal e toda a infraestrutura de condução dos gases emanados durante a evolução do processo.
3.6. Bloco de Resfriamento e Tratamento Mecânico do Sinter
Finalmente, tem-se o setor em que os grandes blocos de aglomerados de sínter são resfriados e fragmentados em tamanhos menores, adequados ao processo subsequente a que será destinado.
4. Variáveis de Controle e sua Importância
Em cada um dos seis setores descritos anteriormente, existem variáveis que devem ser supervisionadas, motivando ações de controle para se atingir um desempenho de máxima satisfação em termos de qualidade e custo do produto final.
4.1. Ensilamento e Dosagem de Matérias-Primas
As variáveis de controle que devem ser constantemente supervisionadas são:
- Nível de matérias-primas nos silos;
- Vazão mássica individual das matérias-primas;
- Vazão mássica da mistura preliminar produzida.
4.2. Mistura e Micropelotização
É o setor onde se procede a mistura de homogeneização seguida de ações de pelotização. As variáveis a serem supervisionadas são:
- Rotação do misturador;
- Inclinação;
- Vazão de água;
- Teor de umidade da mistura;
- Tempo de residência.
4.3. Ensilamento e Carregamento da Mistura Pronta
É uma atividade realizada por um silo, do tipo pulmão, acoplado a um conjunto extrator da mistura por um sistema de rolo ou correia. Neste setor, as variáveis que devem ser supervisionadas são:
- Nível da mistura no interior do silo;
- Abertura de comporta e velocidade de extração;
- Inclinação da placa defletora de distribuição de mistura.
4.4. Ignição da Mistura a Sinterizar
O processo de sinterização é desencadeado, termicamente, através de um forno de ignição onde é promovida a combustão (GLP, gás natural, gás de coqueria, óleo, etc) em contato com o ar atmosférico. A atmosfera de combustão obtida deve conter um determinado teor em excesso de oxigênio, visando ao acendimento do combustível sólido presente na mistura a sinterizar.
As variáveis de controle e supervisão neste setor são:
- Vazão de combustível;
- Vazão do ar;
- Relação ar/combustível;
- Tempo de ignição (no caso do processo intermitente);
- Temperatura do forno;
- Procedimentos de segurança necessários ao equipamento.
4.5. Setor de Sinterização
No caso do processo intermitente neste setor, as variáveis de controle são:
- Altura de camada (variação limitada);
- Depressão sob as caixas;
- Depressão no duto de entrada do exaustor.
Deve-se também acompanhar as variáveis de monitoramento:
- Temperatura dos gases nos dutos de exaustão;
- Temperatura final nos gases de sinterização (sob as caixas);
- Tempo de sinterização;
- Temperatura do exaustor principal;
- Corrente do motor de acionamento do exaustor principal;
- Eventual análise dos componentes dos gases;
- Teor de particulados no gás de exaustão;
4.6. Resfriamento e Tratamento Mecânico do Sínter
As variáveis deste setor são de regulagens com tempos de resposta alongados, usando como feedback as informações de temperatura do sínter bruto transportado e os ensaios e testes realizados posteriormente em lotes de amostras regularmente coletadas.
As variáveis de controle deste setor são:
- Abertura da válvula de abastecimento de ar ou água do resfriador;
- Altura da camada de sínter sendo resfriada;
- Abertura de britadores;
- Inclinação de peneiradores;
- Taxa vibracional dos peneiradores.
Um registro importante deve ser a pesagem do sínter produto, buscando orientar as operações anteriores encadeadas na manutenção das metas de produtividade estabelecidas.
5. Considerações sobre a Informatização e Automação dos vários Subsistemas
INFORMATIZAÇÃO
5.1. Ensilamento e Dosagem de Matérias-Primas
Neste subsistema, é desejável o registro dos valores e dados de todas as variáveis envolvidas:
- Silos: gráficos de evolução das médias, por período, dos pesos por silos, ocorrências de alarmes e situações anômalas;
- Correias dosadoras: gráficos de evolução das médias, por período, dos pesos sendo abastecidos para a correia de mistura total, por silo, além de todas as ocorrências de alarmes e situações anômalas;
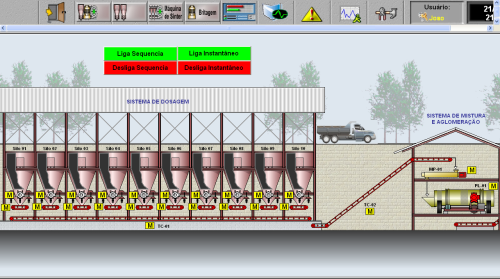
Figura 1: Sistema de Dosagem
- Correia de mistura: gráficos de evolução das médias, por período, da vazão mássica total da mistura sendo transportada e todas as ocorrências de alarmes e situações anômalas.
5.2. Mistura e Micropelotização
Neste subsistema, também é desejável o registro dos valores e dados de todas as variáveis envolvidas:
- Vazão de água: registro em gráficos da evolução média das vazões da água de umidificação, por período, do setor de micropelotização e todas as ocorrências de alarmes e situações anômalas;
- Umidade: caso estas duas operações básicas (mistura e micropelotização) sejam executadas por um único equipamento, deve-se registrar os gráficos de evolução do teor de umidade da mistura pronta para sinterizar, além de todas as ocorrências de alarmes e situações anômalas;
- Outras variáveis: somente o registro de médias de valores, por período, de rotação, inclinação e demais variáveis de operações eletromecânicas, além de todas as ocorrências de alarmes e situações anômalas.
5.3. Ensilamento e Carregamento da Mistura Pronta
- Silo de mistura: gráficos de evolução das médias, por período, dos valores de níveis, ocorrências de alarmes e situações anômalas;
- Comporta de descarga: registro, por período, da dimensão de abertura;
- Rolo ou correia alimentadora: gráficos de evolução das médias, por período, da velocidade de rotação, além das ocorrências de alarmes e situações anômalas;
- Chapa defletora: registro, por período, do ângulo de inclinação.
5.4. Ignição da Mistura a Sinterizar
- Alimentação do combustível: registro em gráficos da evolução média das vazões e pressões do combustível, por período, além de todas as ocorrências de alarmes e situações anômalas;
- Alimentação do ar de combustão: registro em gráficos da evolução média das vazões e pressões do ar soprado, por período, além de todas as ocorrências de alarmes e situações anômalas;
- Tempo de ignição: registro em gráficos da evolução média dos tempos decorridos entre o início e o término da ignição por período;
- Temperatura do forno de ignição: registro em gráficos da evolução média da temperatura do forno, por período, além de todas as ocorrências de alarmes e situações anômalas;
- Segurança operacional: registro de todas as ocorrências de alarmes, desligamento ou anomalias durante o período de ignição.
5.5. Setor de Sinterização
- Altura da camada a sinterizar: registro em gráficos da evolução média das alturas de camada, por período, além de todas as ocorrências de alarmes e situações anômalas;
- Depressão sob as caixas: registro em gráficos da evolução média das depressões sob as caixas, por período, além de todas as ocorrências de alarmes e situações anômalas;
- Depressão no duto do exaustor: registro em gráficos da evolução média das depressões no tubulão que liga as caixas ao exaustor, por período, além de todas as ocorrências de alarmes e situações anômalas;
- Abertura do damper principal: registro em gráficos da evolução média da abertura do damper do exaustor principal, por período, além de todas as ocorrências de alarmes e situações anômalas;
- Temperatura dos gases no tubulão: registro em gráficos da evolução média das temperaturas no tubulão que liga as caixas ao exaustor, por período, além de todas as ocorrências de alarmes e situações anômalas;
- Temperatura sob as caixas de sinterizar: registro em gráficos da evolução média das temperaturas nas pernas de vento, por período, além de todas as ocorrências de alarmes e situações anômalas;
- Tempo de sinterização: registro em gráficos da evolução média dos tempos decorridos entre o final da ignição e a liberação para basculamento, por período, além de todas as ocorrências de alarmes e situações anômalas;
- Temperatura exaustor principal: registro em gráficos da evolução média da temperatura da carcaça do exaustor principal, por período, além de todas as ocorrências de alarmes e situações anômalas;
- Corrente do motor do exaustor principal: registro em gráficos da evolução média da amperagem do motor do exaustor principal, por período, além de todas as ocorrências de alarmes e situações anômalas;
- Eventual análise dos componentes dos gases: registro em gráficos da evolução dos teores de CO, CO2, N2, NOx e SOx nos gases de exaustão, por período, além de todas as ocorrências de alarmes e situações anômalas;
- Teor de particulados no gás de exaustão: registro em gráficos da evolução dos teores de particulados nos gases de exaustão, por período, além de todas as ocorrências de alarmes e situações anômalas;
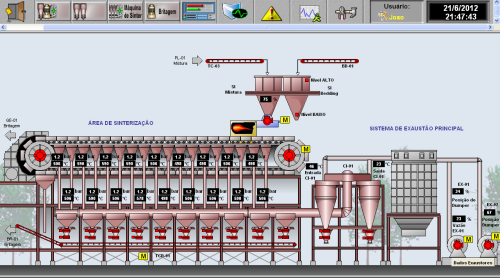
Figura 2: Máquina de Sinter
5.6. Resfriamento e Tratamento Mecânico do Sínter
- Abertura da válvula de abastecimento de ar ou água do resfriador: registro em gráficos da evolução média da abertura do damper ou válvula de água usada para o resfriamento do sínter bruto, por período, além de todas as ocorrências de alarmes e situações anômalas;
- Vazão de água de resfriamento: em caso do uso exclusivo de água para o resfriamento do sínter, registro em gráficos da evolução média da vazão de água usada para o resfriamento do sínter bruto, por período, além de todas as ocorrências de alarmes e situações anômalas;
- Altura da camada de sínter sendo resfriada: em caso de resfriador plano, registro em gráficos da evolução média da altura da camada do sínter bruto, por período, além de todas as ocorrências de alarmes e situações anômalas;
- Nível do silo de sínter sendo resfriado: em caso de resfriador tipo silo, registro em gráficos da evolução média do nível do sínter bruto, por período, além de todas as ocorrências de alarmes e situações anômalas;
- Abertura de britadores: registro em gráficos da evolução média da abertura dos britadores (mandíbula e/ou rolos), por período, além de todas as ocorrências de alarmes e situações anômalas;
- Inclinação de peneiradores: registro em valores da inclinação dos peneiradores, por período, além de todas as ocorrências de alarmes e situações anômalas;
- Taxa vibracional dos peneiradores: registro em gráficos da evolução média da frequência vibratória dos peneiradores, por período, além de todas as ocorrências de alarmes e situações anômalas;
- Pesagem do sínter produto: registro em gráficos da evolução das vazões mássicas do sínter produto sendo transportado ou ensilado para os clientes, por período, além de todas as ocorrências de alarmes e situações anômalas;
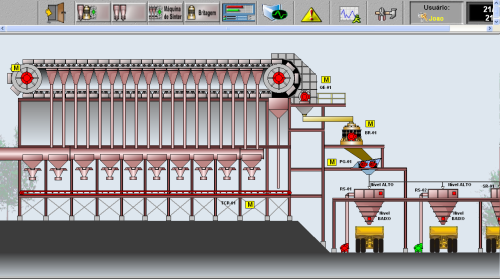
Figura 3: Britagem
AUTOMAÇÃO
Existem basicamente três filosofias de automação passíveis de serem implementadas em uma unidade de sinterização:
- Automação de subsistemas autônomos;
- Automação global com integração dos subsistemas utilizando o método Guia de Operador;
- Automação global com integração dos subsistemas em loop fechado.
Basicamente, todos os subsistemas podem ser submetidos a todas as filosofias de controle automático descritas acima.
Os fatores que definirão o melhor para uma determinada unidade são: o valor que o empresário estará disposto a investir, e a disponibilidade de mão de obra qualificada e especializada para a operação e manutenção da instrumentação e equipamentos envolvidos.
Certamente, a cada nível mais aprofundado de automação, a relação custo/benefício poderá ser reduzida tornando-se cada vez mais atraente. Modernamente, a filosofia mais adotada por pequenos e médios produtores é de automação dos subsistemas, com uma supervisão humana local por blocos. Assim, por exemplo, pode-se automatizar os subsistemas:
1 – Ensilamento e dosagem de matérias-primas;
2 – Controle de umidade da mistura a sinterizar;
3 – Controle de nível de silo e velocidade do sistema de carregamento da mistura a sinterizar;
4 – Controle do nível de depressão sob as caixas de sinterização;
5 – Controle da temperatura do sínter bruto resfriado.
Pode-se considerar coordenadores de área por turno, acompanhando os subsistemas 1, 2 e 3, e outros acompanhando os subsistemas 4, 5 e o conjunto de tratamento mecânico. Obviamente, deve-se ter o apoio de coordenador(es) locados no painel central onde são direcionadas todas as informações coletadas pela instrumentação e são feitos os processamentos de dados, buscando resumir eficazmente as indicações disponibilizadas.
Na filosofia Guia de Operador, o número de pessoas necessárias, circulando pelas áreas dos subsistemas, é bem reduzido. Assim, toda a tarefa de monitoramento e tomada de decisões acaba ficando centralizada no painel de controle onde se pode necessitar de um pouco mais de pessoas. A filosofia do loop fechado talvez seja mais indicada, com algumas restrições, para a supervisão das unidades de grande porte e com operação contínua, como no processo Dwight & Lloyd.
A MAS ENGENHARIA, utilizando o software ELIPSE E3, solução SCADA desenvolvida pela empresa brasileira Elipse Software, vem conseguindo obter grandes benefícios e vantagens nos processos de sinterização. Através dos recursos do Elipse E3, a MAS Engenharia detém o registro de todos os dados necessários à informatização e controles relacionados ao processo de automação, sejam eles pertinentes ao processo de automação de subsistemas autônomos, automação global, automação utilizando o operador, ou automação global em loop fechado. Em todos os casos, é notório o aumento da qualidade do produto final através do controle das variáveis de processo, assim como a redução do número de operadores necessários para operar a planta.
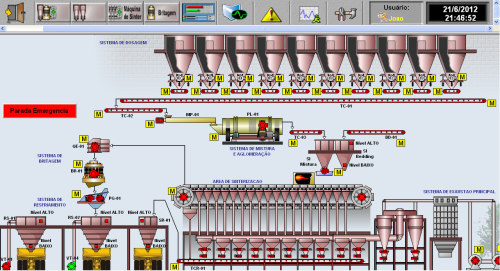
Figura 4: Fluxograma de funcionamento de uma sinterização contínua tipo DWIGHT & LLOYD